My Dunster House log cabin build – part 2
This is the second part of my post describing my experiences building a Dunster House Log Cabin in our back garden. The first part of this series can be found here.
Dunster House log cabin Day four build
In contrast to day three, when the build seemed to progress rapidly, on day four the log cabin hardly seemed to change at all.
I started by adding the remaining roof boards which covered the canopy at the front of the log cabin. This had been a quite quick operation when I was adding the boards to the main building because I could position ladders on the solid concrete base, but the ground below the canopy is muddy and uneven, so this took longer than I expected. It also didn’t help that the temperature had dropped a few degrees (to about 3C), and I had started to get splits in the skin on my thumbs which, added to some chilblains, made it quite painful to work.
The final two roof boards needed to be cut down their length to get the boards to line up with the end of the purloins, and this also caused some delay as I had to hunt around for a saw which was set up for a rip cut1.
Once I’d eventually got the rest of the roof boards on, I added the reinforcing trim to the edges of the roof. This is a thin batten of wood which runs round the edge of the roof and adds some thickness to strengthen the edges.
At this point, the next operation should have been to add the insulation board to the roof. These are boards with thermal insulation bonded to a chipboard board, which are screwed to the roof boards to provide insulation against heat loss.
The boards are supplied in standard sizes and there is a fitting / cutting plan in the instructions showing how they are laid out.
However, by the time I’d got to this point it was about 2:30 pm, and I was concerned that I’d not have time to get all the boards on the roof, and get a protective plastic sheeting over them before it got dark. I didn’t want the possibility of the chipboard being soaked with condensation and being damaged overnight.
For this reason, I switched to the inside and started to lay down the floor.
The flooring consists of tongue and groove boards which are nailed to the bearers which support the cabin, with a layer of thermal insulation placed between the bearers underneath the boards.
This was the point that I discovered an issue with the way I’d constructed the log cabin.
Basically I found that the bearers, which I’d supported on joist supports to compensate for the uneven concrete slab I’d prepared, were now not level across the whole of their length. Because the weight of the log cabin walls was pushing down on the two ends, the middle of the bearers were bending upwards, and the joist supports were lifted above the ground.
Because I’d fitted the joist supports about 3 inches in from the end of the bearers, which would tend to exacerbate this, I moved them further along towards the end2, and although this helped, it didn’t completely remove the issue.
At first, I hoped that once I started nailing down the floor boards and applying some weight, this would correct itself, but I found as I added more floor boards the effect became more pronounced, and the boards started to split as the bending force applied.
Because I needed to get the main cabin construction finished and weather protected, I decided to deal with the floor once I’d completed the rest of the cabin, and I’ll describe my solution in the last post in the series.
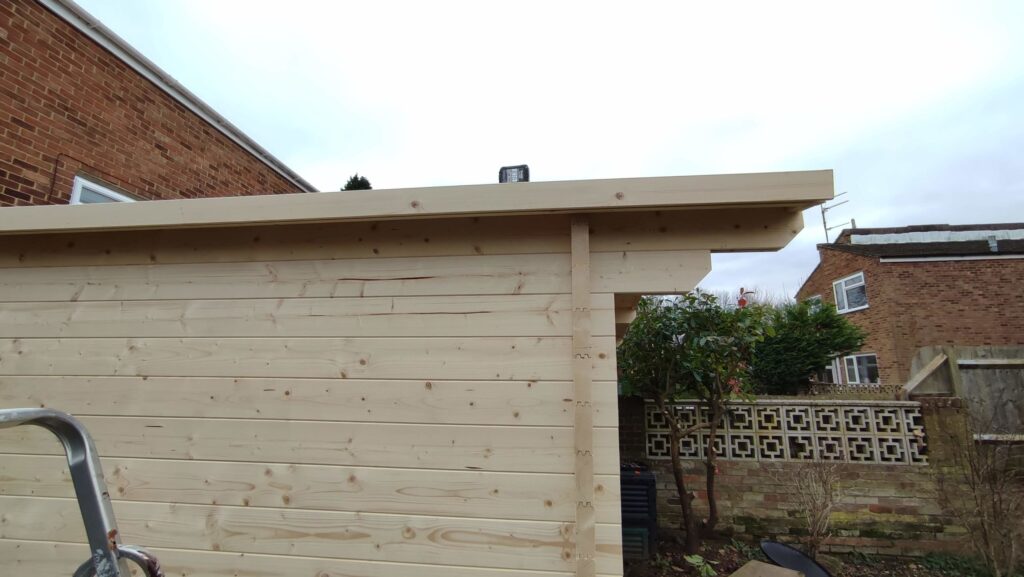
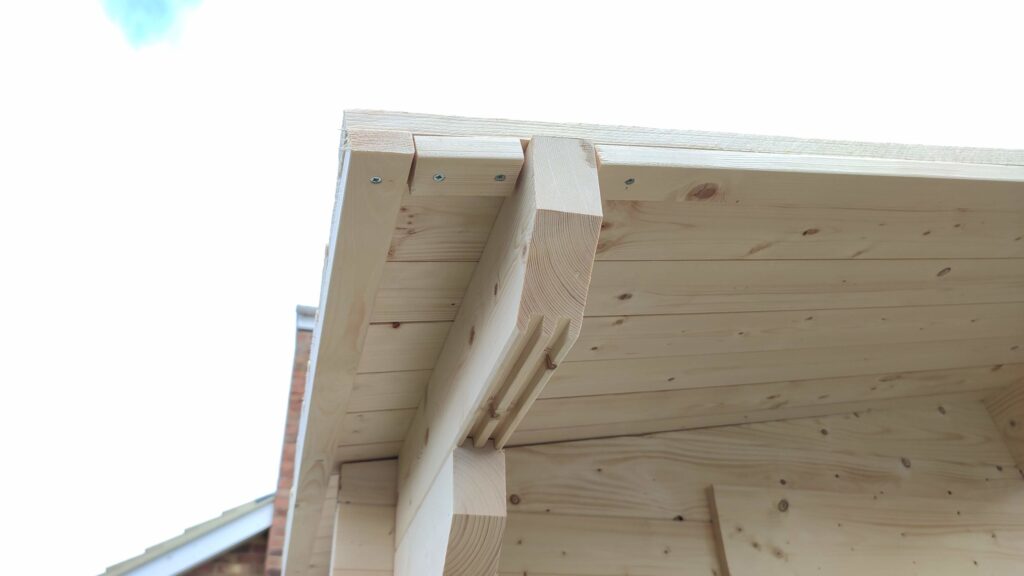
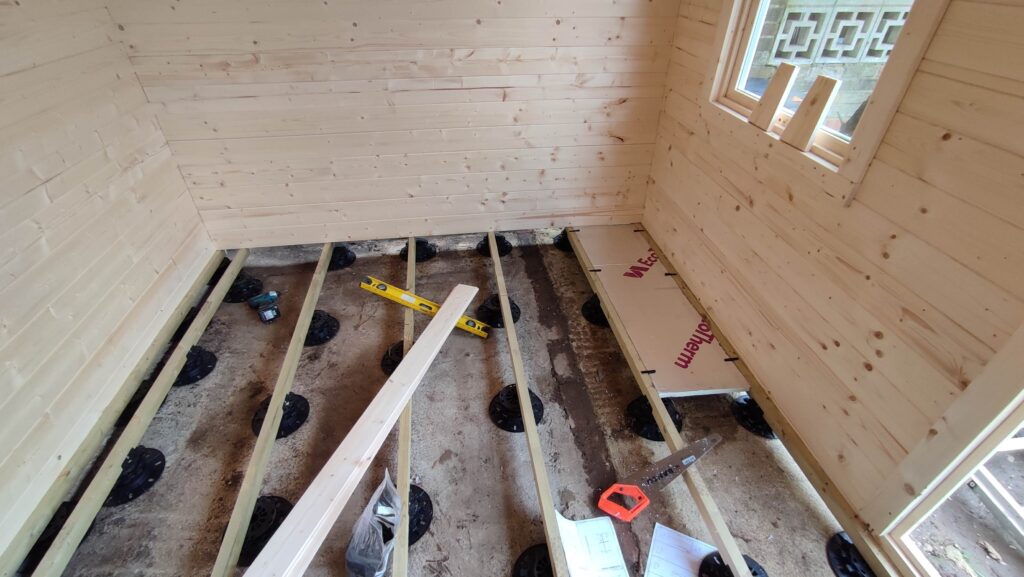

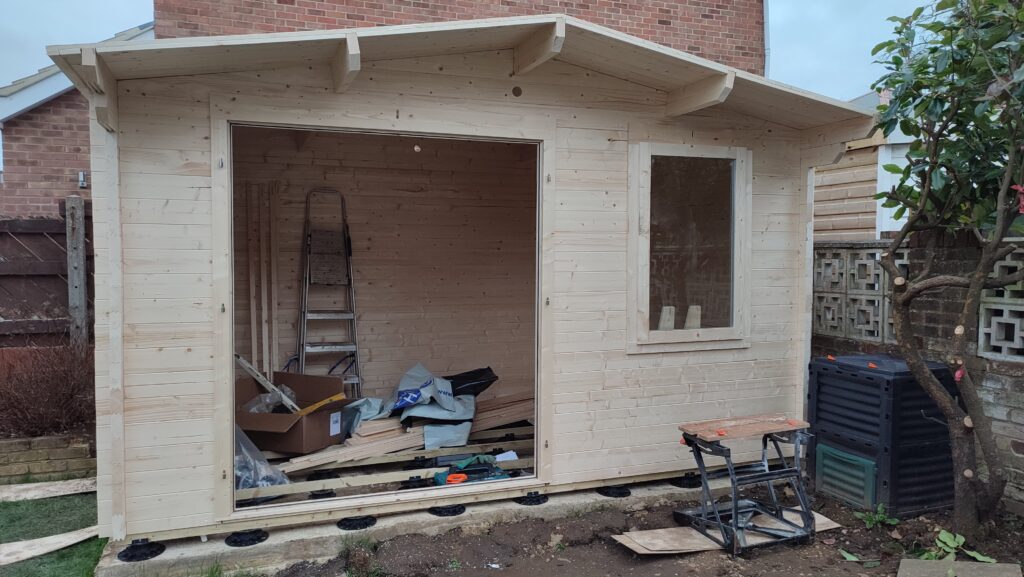
Dunster House log cabin day five build
On Day five, I concentrated on getting the roof insulated and water tight.
The first thing was to fit the insulation boards, described above, to the roof. For the model of Dunster House log cabin I was building there are two large boards measuring about 1.2 M x 2.4 M, 5 long thin boards measuring about 2.4M x 0.45 M and one board 2.4 M x 0.62 M. Included in the plans was a diagram showing how these boards need to be cut to be fitted to the roof.
The first problem I had was that I couldn’t lift the largest boards up onto the roof by myself, they were simply too heavy. I got round this by using a track saw to cut the boards in half and push each half up on to the roof, where I could lay them next to each other to make up the original board size.
Once the boards were physically positioned on the roof boards, they are screwed around the edges using 50mm screws. The instructions make it plain that the screws should only be screwed to the depth of the board because they are only 4 mm shorter than the combined depth of the insulation board and roof board.
With the insulation in place, I next fitted the wooden edging bar to the sides of the log cabin. These are strips of wood which neaten up the side and are attached by metal angle brackets which screw into the newly fitted insulation boards.
With all the insulation fitted and the side rail in place, the next step was to make the roof water tight.
The weather proofing consists of a thin plastic membrane which initially covers the whole roof surface, and then this is covered with a set of shingles. The shingles are supplied as long felt tiles which consist of three shingles and these are used to cover the roof in an overlapping series of rows which leave a very attractive, and fully water tight roof. As far as I can see, there is a row of bitumen glue on the tiles which melts in the summer sun to fuse the tiles together.
Fitting the plastic membrane was more difficult than the shingles turned out to be in many ways because Dunster House supplied it in a plastic roll, and it had many creases permanently set into it. This made it difficult to get flat on the roof, and also difficult to unroll by myself whilst standing on the roof.
In the end, I calculated that the width of the roll was wide enough to cover the full width of the building, and cut a length that would be sufficient to go over the roof, whilst I was still on the ground. Then I managed to get it pushed out over the roof structure and get some staples in it to hold it in place.
The shingles are added to the roof starting with a row along the bottom edge.
The first row is doubled, with the first layer placed upside down and then another set of tiles added directly over the top. After that row, the next is offset by a half tile and nailed above the first row so only the tiles show.
In order to get the offset, the tile is cut in half. I first started doing this from the ‘gritty’ side of the tile, but I found if it’s turned over and cut from the back it is both a much cleaner cut, and considerably easier to do.
By the end of the day I had about 3 rows of tiles placed on the first side of the log cabin, but I forgot to take a photo, so the photo shown here was actually taken the next day when I completed the roof.
Day five photos
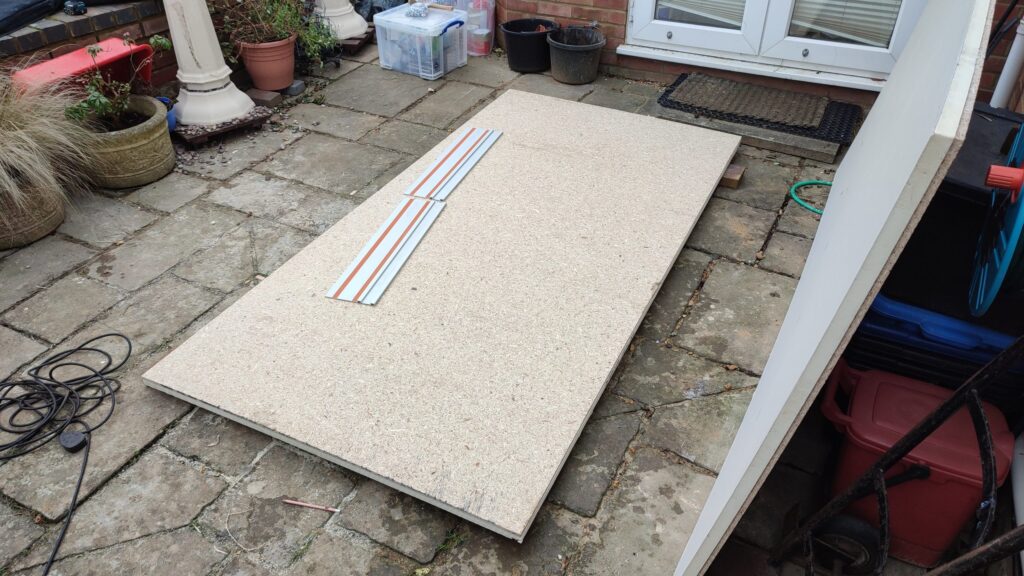
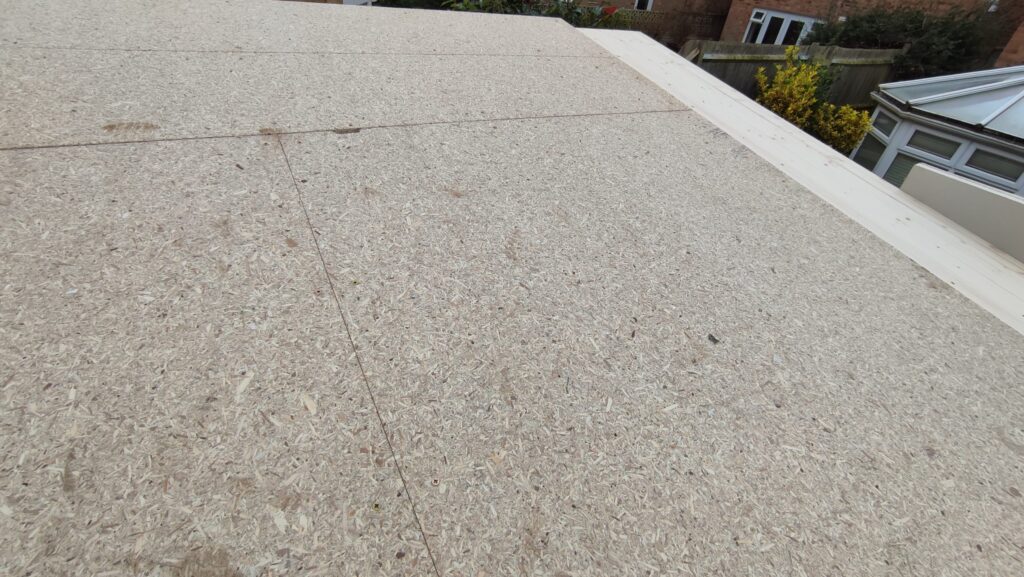
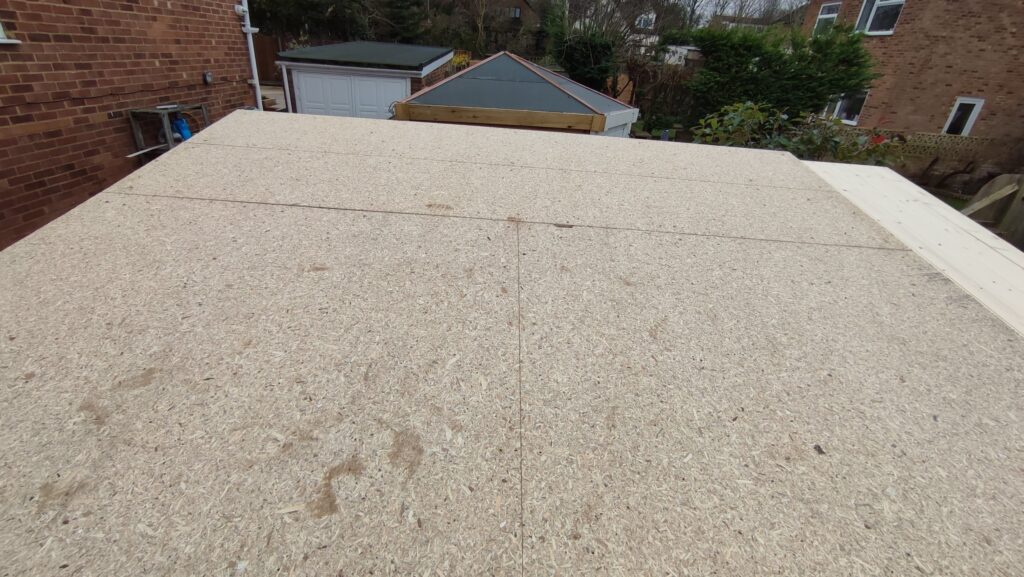
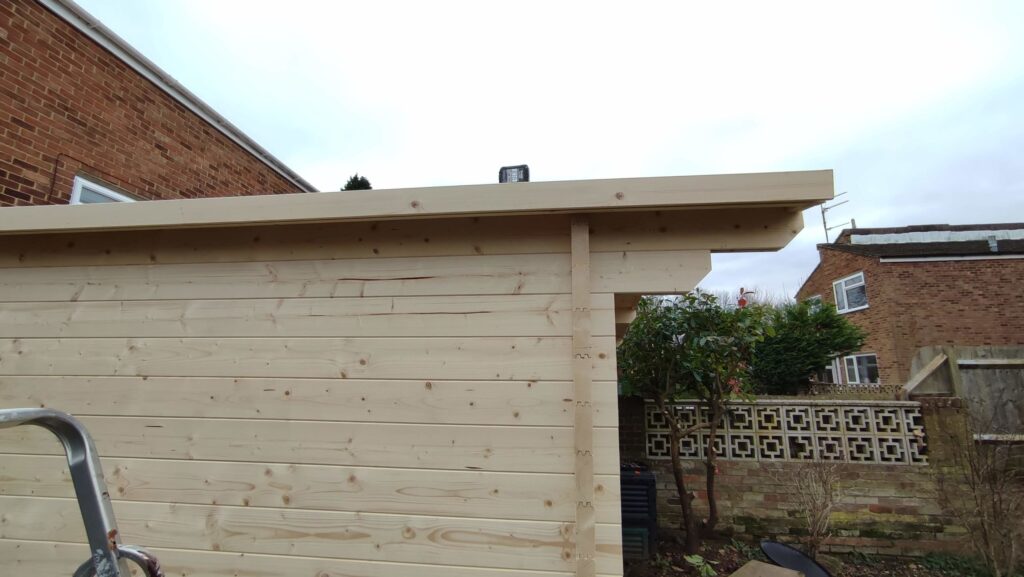
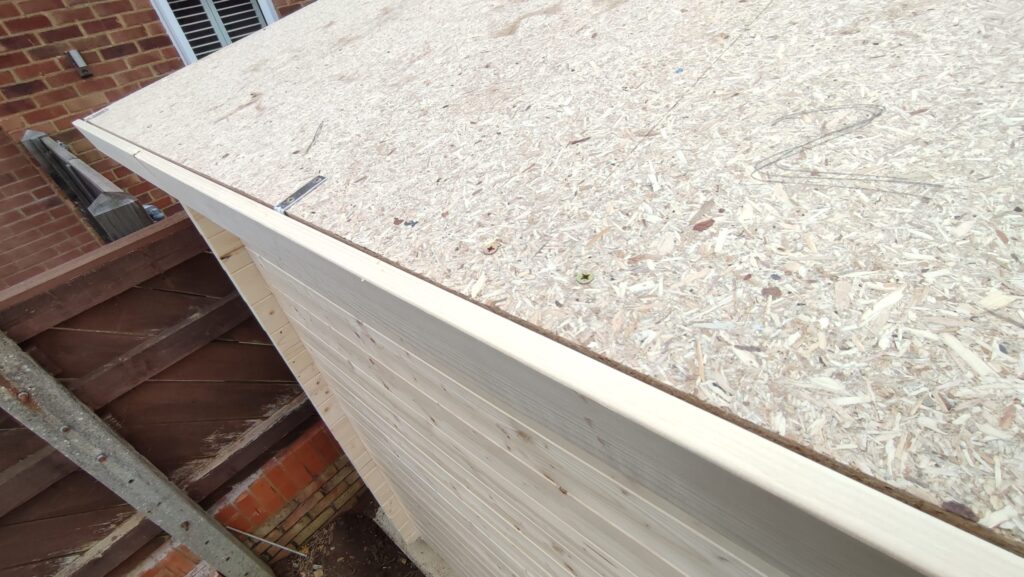
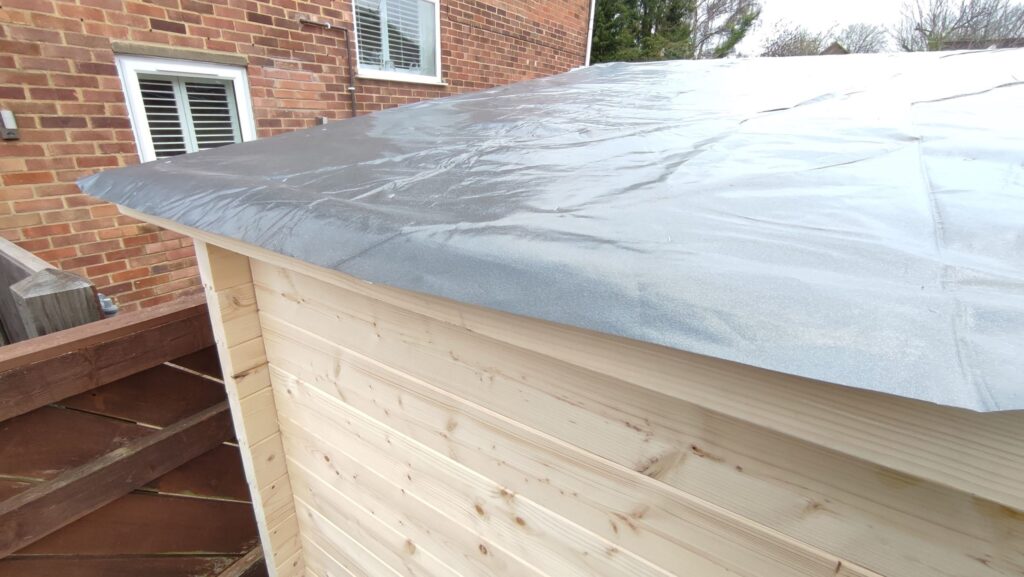
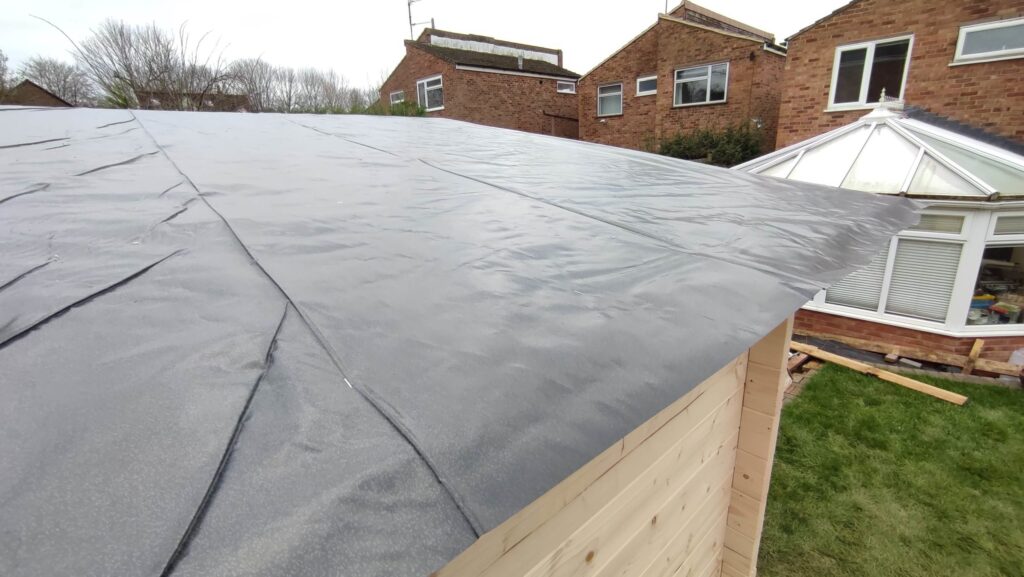
Dunster House Log cabin day six and seven build
The main activity on day six was the completion of the roof shingles.
Because the first row of shingles overhang the edge of the log cabin, I had to clamp a piece of 3×2 wood to the side rail, so I could get a ladder up against the building to get access to the roof. With that in place, I pushed a number of shingle tiles up (which wasn’t easy because they are quite heavy), and then spent the rest of the morning adding rows of shingles until I met the roof apex on one side.
Adding shingles to the opposite side of the roof was more tricky. Although I have arranged that there is access to the side for painting etc, I can’t get a ladder on that side because it’s too close to the neighbour’s wall. Also, my neighbour has a summer house on his side, and even if I went round his side the angel of the ladder would be wrong to gain access. This meant I had to apply the shingles whilst positioned on the roof, working down the slope.
I managed to do this, but it wasn’t comfortable applying the first 3 or 4 rows, working down the slope. Fortunately, by the 5th row, I could kneel on the shingles I’d just added and work more conventionally.
Once I had both sides of the roof shingled, the apex is formed by cutting the remaining shingles into individual tiles and using them to cover the gap as shown in the photo here.
The rest of day six and all the time I could spend on the build on day seven was taken up applying paint to the building. The paint supplied by Dunster House if a very good quality paint by Protek which requires two coats of a primer and then coats of the top coat colour.
Initially, I was concerned that there wouldn’t be enough paint supplied to cover the building – not because of any real rational fear, but just because often companies cut corners on this sort of thing. That fear turned out to be groundless however, because Dunster House supplied 8 litres of both primer and top coat colour, and after priming the whole log cabin with two coats and applying the colour to the main cabin (the windows and doors will be a different colour), I still have 5 litres of each left over.
Day six photos
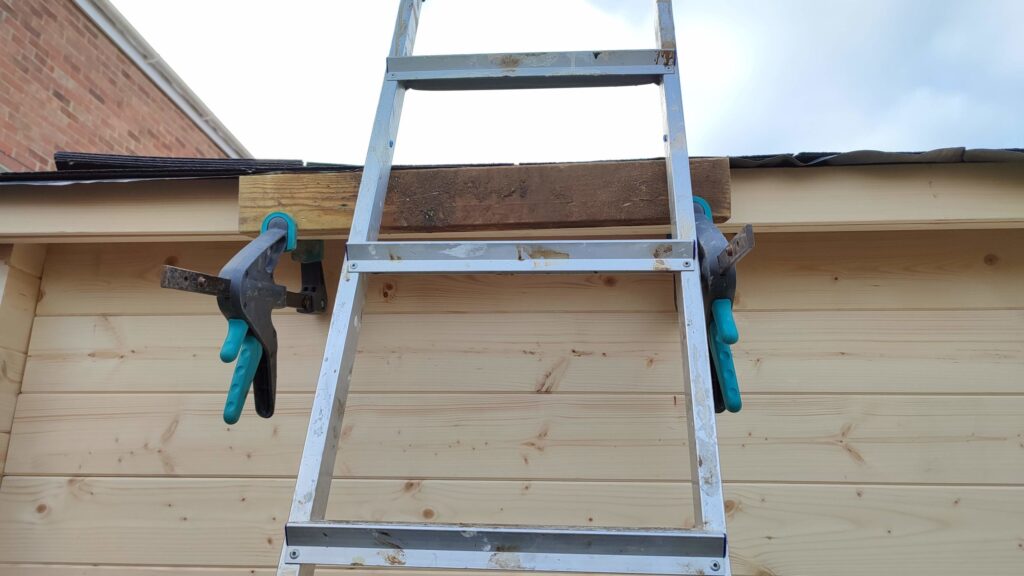
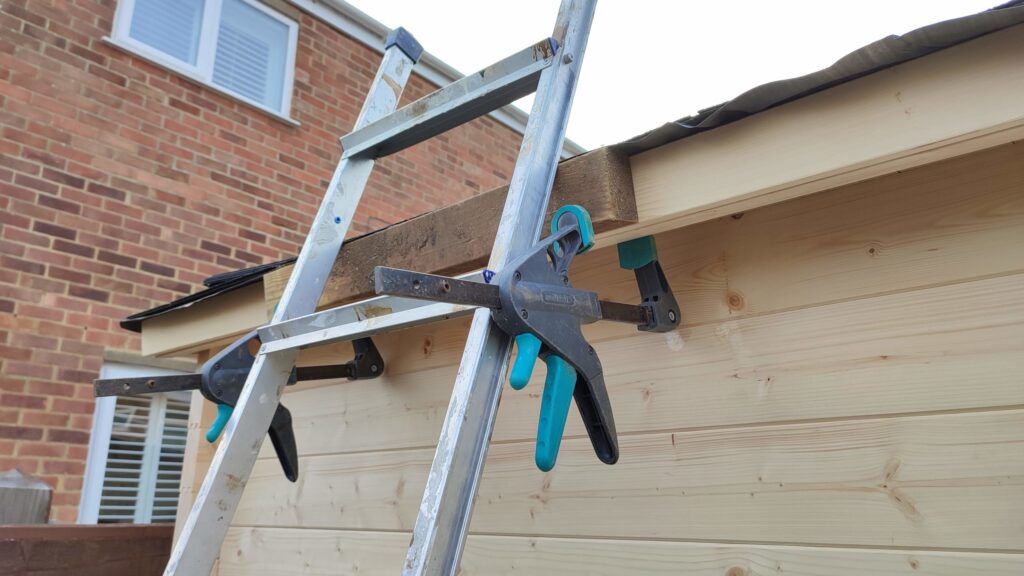
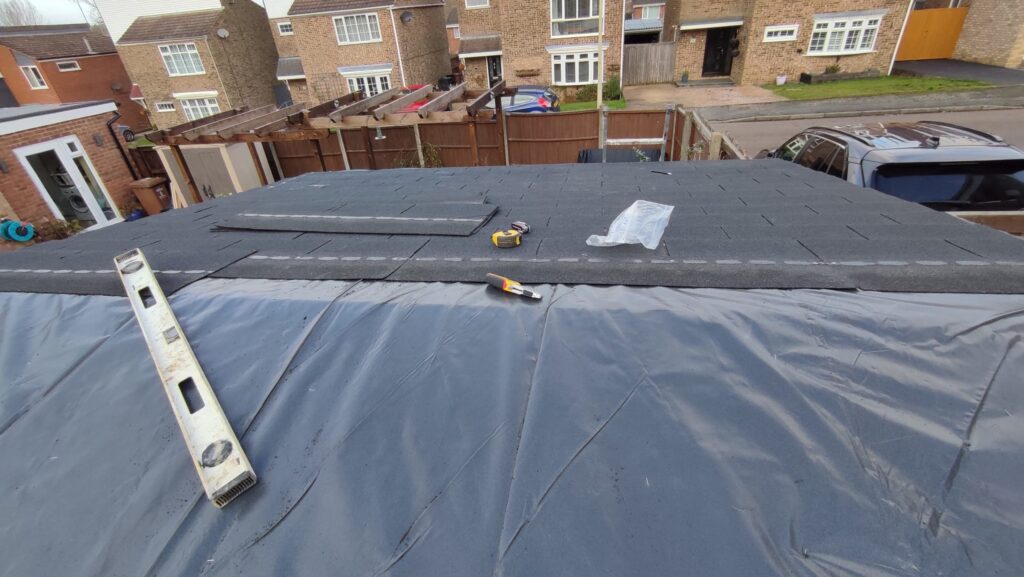

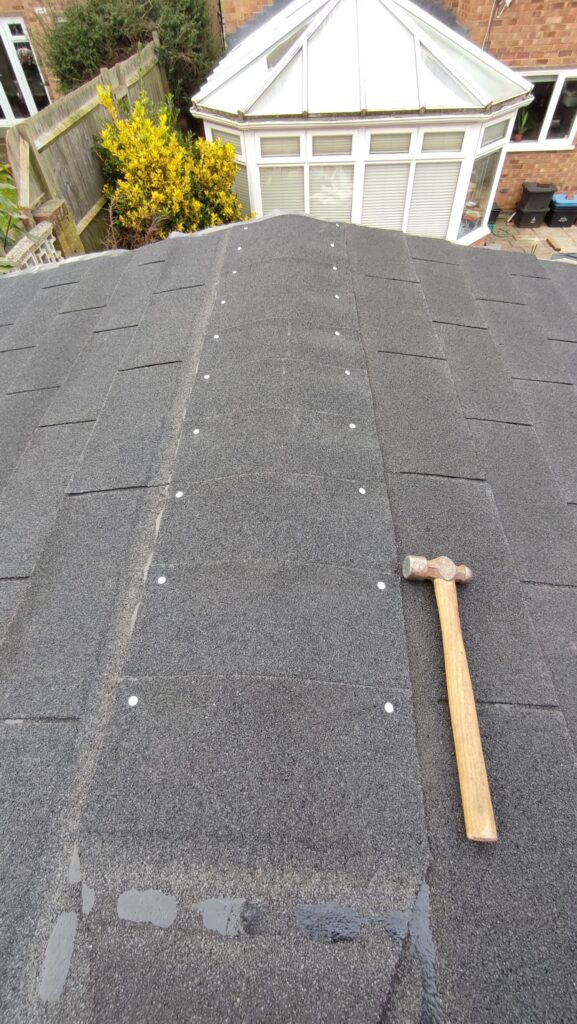
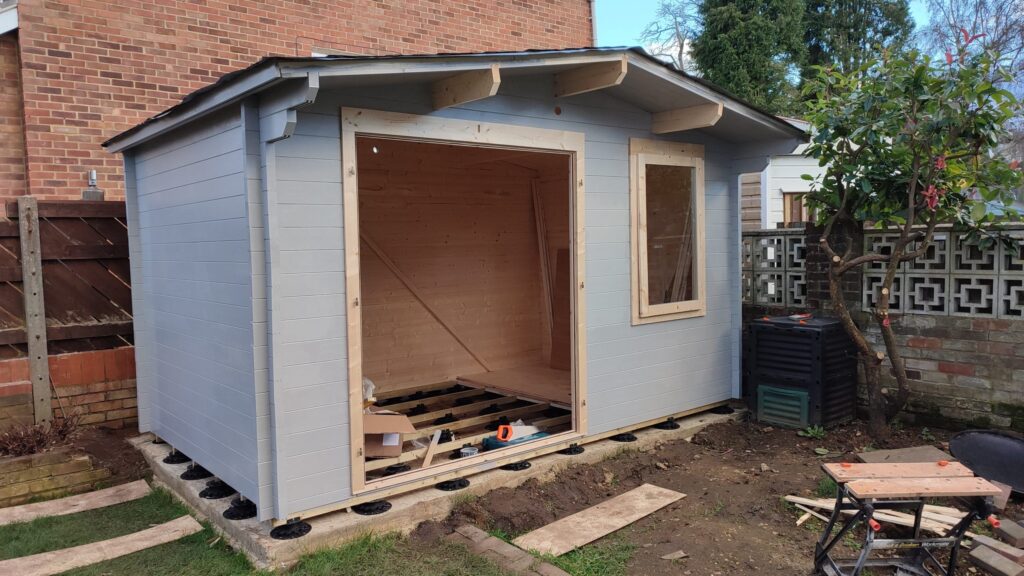
At the moment, the two posts in this series cover the progress of the build completely up to date. In a few weeks, once I’ve completed the last few bits and pieces which need to be finished and dealt with the floor issue, I’ll write a final post describing those last issues and my overall impressions of the log cabin.
Update: The next part of this series which describes how I fixed the floor issue and completed the build is here.
- All my tools are currently packed in the conservatory whilst I construct the log cabin, so although I’d assembled a basic tool kit I needed to search for a rip cut saw [↩]
- I did this carefully by unwinding the support before removing it and replacing it at the end of the bearer and re tensioning it [↩]